technological achievements
technological achievements
-3200威尼斯vip
发布时间:
2017-05-04 13:06
我国钢铁工业在过去十年间的吨钢能耗逐年下降,节能工作取得了显着的成就,但依然存在一些问题,在下一步发展中面临严峻的挑战,其中很重要的一个方面就是余热余能的利用问题。
钢铁工业制造流程是一个大规模能源循环系统,在构成该系统的工序内部,在各工序之间进行复杂的能量消耗、转换、再生、输送,而且钢铁联合流程具有很强的热管理特征。
钢铁生产消耗的一次能源中约40%以某种形式的热能释放出,其温度上至1500℃,下至近于环境温度的广泛范围。目前我国生产1吨钢产生的余热余能资源量约为8gj~9gj,主要分为副产煤气、排气余热、固体余热及废汽废水余热。副产煤气包括高炉煤气、焦炉煤气及转炉煤气,一般归为余能,但其显热及压力能属于余热;排气余热多为炉窑排出废气带走的热,占余热资源总量的一半左右,温度范围为250℃~1000℃;固体余热包括烧结矿、红焦炭、高炉渣、转炉渣及铸坯等的余热,一般在500℃以上;废汽废水余热包括蒸汽冷凝水、锅炉汽包的排污水(90℃~100℃)、高炉冲渣水(70℃~90℃)等的余热。
余热余能利用获得大发展
余热余能利用技术广泛应用。近年来,钢铁工业余热余能利用技术得到广泛应用:其中,重点大中型企业的干式trt配备率已经超过90%,吨铁发电量高已经超过50kwh;重点大中型企业干熄焦比例达到42.3%,吨焦炭回收蒸汽高超过570kg;吨烧结矿回收蒸汽高超过70kg;燃气-蒸汽联合循环发电机组(ccpp)作为高效的能源转换装置,在行业内迅速推广,包钢、莱钢、太钢、沙钢等近20家钢铁企业均建有ccpp。
此外,饱和蒸汽发电、蓄热式加热炉烧低热值高炉煤气技术、连铸坯热送热装、高炉冲渣水余热利用、转炉汽化冷却蒸汽直供rh等技术在行业内广泛应用,煤调湿技术、焦炉上升管余热利用、热导油蒸氨等技术也有所突破。
煤气损失率逐年降低。近年来,高炉、焦炉、转炉煤气的利用量逐年提高,损失率逐年降低。与2006年相比,2010年焦炉煤气损失率降低了0.96个百分点,高炉煤气损失率降低了2.65个百分点,转炉煤气损失率降低了11.25个百分点。
自发电比例不断提高。(楷体)钢铁行业余热余能综合利用水平和自发电比例不断提高,自发电比例由2006年的21.6%上升到2010年的31.9%,提高了10.3个百分点。邯钢、唐钢等企业的自发电比例超过了70%。
传统回收方式问题有待解决
虽然近年来钢铁工业的余热余能利用取得了一定的成就,但是余热余能本身具有布局分散、品质参差不齐的特点,造成了以传统方式回收利用能源存在一定问题。而且二次能源生产总量总要大于消费量,在一定程度上存在能量供、需不匹配。目前,钢铁工业余热余能利用普遍存在如下问题:
一是往往重视余热余能的回收而轻视利用效率,造成了严重的无效回收。例如副产煤气的回收都经过煤气除尘设施和煤气加压输配设施,消耗了一定的成本,如回收的煤气没有找到合适的用户而放散,这就是严重的无效回收现象。
二是传统的能源回收利用普遍采用长距离输送方式,造成能流传输能耗高、传输损失大。例如长距离输送中低温的饱和蒸汽,会造成大量热损失,不仅使回收能源又浪费掉,还会造成软水流失形成新的损失。
三是蒸汽系统没有得到高效利用,钢铁企业目前普遍存在蒸汽大量放散现象,尤其是夏季,有很大的回收利用空间;与此同时,往往热电配减温减压器供蒸汽管网,中间环节没有任何对外做功过程,能量贬值非常大。
四是部分耗能设备介质使用不合理,没有做到能级匹配和温度对口。由于部分企业缺乏统一的用能管理及经济调节措施,使得各用能工序纷纷争抢优质能源,往往就造成了高能低用的现象,从全局的角度来看能效低下。
应对新形势下的挑战
钢铁工业面临新的发展形势,余热余能利用也面临着新的挑战。
煤气损耗有待进一步降低。尽管钢铁行业煤气放散率逐年下降,但由于生产规模增加导致煤气损耗的数量仍然偏大,副产煤气利用的节能潜力尚未完全发挥出来。这给钢铁工业节能工作带来了新的挑战,需要根据煤气资源的数量、品质和用户需求不同,合理分配使用煤气,完善煤气缓冲系统,进一步降低煤气的放散损失率。
煤气利用方式须根本性转变。随着低碳经济时代的到来,企业传统的余热余能单一转化为电能的利用方式将面临着转型,如何实现“资源—能源—再资源”综合利用将是进一步提高能效的关键所在。焦炉煤气作为一种优质的二次能源,可以生产氢气、甲醇、二甲醚等,待工艺成熟时候也可直接喷吹入高炉,利用焦炉煤气中的h2和ch4进行高炉冶炼,最终实现高碳能源低碳化利用。
热电转换效率进一步提高。各大企业热电机组应该逐步向高温高压参数机组发展,行业内存在相当数量的中温中压机组,阻碍了能源转换效率的进一步提高。企业应结合企业发展规划,整合淘汰小型机组,建设大型高参数发电机组,将能够较大幅度提高企业的自发电水平。
低温余热利用进一步深化及拓展。目前钢铁中、高温余热已基本得以回收,低温低参数余热资源综合利用成为进一步挖掘节能潜力的关键所在,包括高炉冲渣水余热、汽轮机冷却水余热、焦化初冷水余热等,虽然温度较低,但是资源总量相当可观。节能工作者应该根据分布式能源梯级利用的理念,提高余热质量,建设具有一定经济规模效应的地区式热能利用系统;同时注重余热利用的功能拓展,将余热用于海水淡化或污泥处理等。
与城市和谐共融发展。钢铁企业一向以高能耗、高排放形象示人,面对新的节能减排形势,钢铁企业应该全力推动绿色转型,努力做到与城市和谐共融发展,成为城市发展不可分割的部分。以钢铁企业余热余能利用为核心,构建冶金炉窑—副产煤气—共同火力—电力回供,以及冶金炉窑—低温冷却水—城市采暖水等多条循环经济产业链,达成与社会的大循环,实现真正的循环经济。
政策措施进一步完善。余热余能利用的最终形式体现为回收电力,但是我国目前发电上网存在一定的政策障碍,如并网审批困难、过网等费用繁多,影响和限制了钢铁企业利用余热余能的积极性。这给政策制定者提出了挑战,应制定钢铁企业电力并网(上网)的合理政策和价格体系,鼓励钢厂利用余热余能建自备电厂,同时对于余热余能利用项目须进一步加大财政奖励。
节能服务市场化机制进一步完善。目前节能效益明显的重大节能措施在钢铁企业中已经普遍配建,但是一些小节能项目的推广存在一定的障碍。这主要是因为该类项目的投资回收期相对较长,节能效益相对不明显,企业在经营困难时期不愿意投入资金和人力。此时,须充分发挥节能服务市场的优势,利用合同能源管理方式解决企业技术、资金、运行管理等问题,实现共赢。
上一页
上一页
相关科技成果
1066vip威尼斯的联系方式
电话 : /
邮箱:
联系地址:湖北省武汉市江汉经济开发区江兴路17号中信大楼516
办公地址:湖北省武汉市黄陂区卓尔企业社区三期g10栋
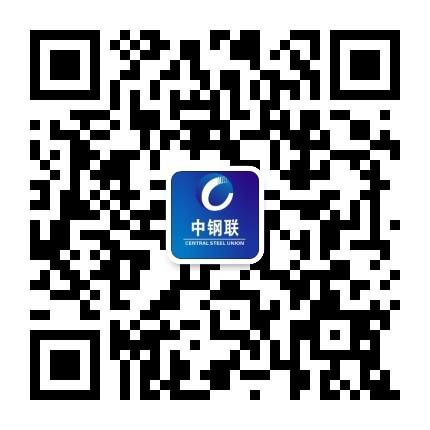
官方微信
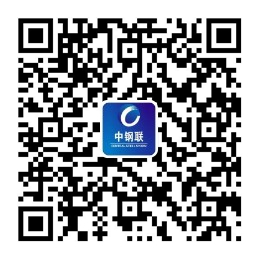
手机网站